Concrete Repair Colorado Springs involves addressing issues affecting the structural integrity of existing concrete. It’s important to figure out what caused the damage and install a repair that will last.
Concrete patches should have a low coefficient of thermal expansion to avoid shrinkage cracking. It also must be able to bond well with the existing concrete.
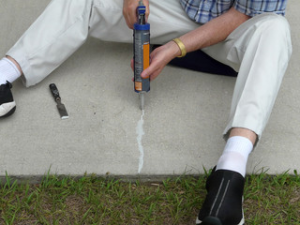
Epoxy injections are an excellent solution for repairing non-moving cracks in concrete walls, slabs, and columns. They help eliminate movement of concrete during expansion and contraction, restoring the structural strength of the structure. Injections can also seal leaking cracks. However, it is important to determine the cause of the cracking before attempting this repair method. If the cracks are caused by frequent movement, other methods like internal and external reinforcement may be needed.
First, clean the crack surface using wire brushes and vacuuming. Surface ports are then installed and sealed with Sealboss 4500 crack-sealer epoxy paste. The ports should be spaced a minimum of four (4) to eight (8) inches apart.
Once the ports are installed, dispense the epoxy into the crack using a dispensing tool. A compression spring on the dispensing tool is used to dispense the epoxy slowly and consistently. This helps reduce the possibility of leaks and blow outs. It will be necessary to fill the crack multiple times.
If the epoxy refuses to flow into the crack, it is likely that there is water present in the crack. This most often occurs when the crack expands and/or branches off under the surface of the concrete element. In these situations, longer injection time may not force the polyurethane to the next port. This most likely indicates that the crack is too large for injection or that it requires a gel viscosity injection epoxy.
Hydraulic cement is a common material used in concrete repair. It is a type of cement that creates a waterproof seal and sets incredibly fast, which makes it ideal for plugging cracks in basements and foundations. It is also a common choice for patching up leaks in pipes, as it can stop water flow very quickly.
Hydraulic cement begins as a powder that can be mixed with water to activate the chemical process of hydration. It is often modified with additives that accelerate curing, stop water, or adhere to surfaces more effectively. When it is used in construction and concrete repair, it can be applied in a thick paste to fill cracks or as a coating for surfaces that need protection from water, ice, and chemicals.
While hydraulic cement is a useful option for some situations, it is not the most effective solution for concrete crack repair. When used on its own, it only covers the surface of a crack and is not a permanent solution to structural problems. It also doesn’t bond well with existing concrete, which can lead to further damage and deterioration.
Instead, hydraulic cement should be used as a base for more permanent solutions to concrete crack repair. This includes the use of chemical polyurethane grouts. These are used in applications such as repairing sewer pipe cracks, tunnel or shaft construction, sealing leaking concrete structures, and handling other types of infiltration and inflow problems.
Bonding agents are used to create a strong bond between concrete, steel, and other materials. They usually contain resins, solvents, and additives that work together to create a strong and durable bond. They are different from traditional adhesives, which use a single type of adhesive material.
When choosing a bonding agent, make sure it’s the right one for your job. For example, PVA won’t bond well to concrete, and acrylic latex might not be a good choice for fiddly repairs. You also need to make sure the surface you’re trying to bond is clean and free of debris.
Once you’ve chosen your bonding agent, follow the instructions on the label. Some may need to be shaken or diluted before use, while others can be mixed directly with cement. Once the bonding agent is ready, apply a thin layer to the existing surface. You can apply it using a brush, roller, or sprayer depending on the product.
Epoxy bonding agents are much more expensive than cementitious ones, but they offer incredibly high bonding strengths. Pirro often uses an epoxy-modified cementitious bonding agent that also provides an anti-corrosion coating when doing spall repair. This allows his crew to coat the rebar and the concrete substrate at the same time. It’s important to note that a smooth surface won’t adhere as well, so roughening it can help. A rougher surface will provide more nooks and crannies for the bonding agent to adhere to.
The repair of prestressed concrete can be complex, and a number of factors must be taken into account. The main challenge is that of re-establishing the tensile strength of the prestressed element. This can fail if the original jacking device imparts a tensile force into the tendon that is greater than is safely tolerable for the structural lifetime, or if strand corrosion causes the tendons to lose their preload. In these circumstances it is often necessary to remove the damaged tendons and replace them with identical ones stressed to a lower level.
Prevention of corrosion is key, with silanes or alternative breathable coatings preferably being applied before critical chloride levels reach the strands. However, if corrosion has already occurred the options for repair are limited. In this case the deteriorated strands must be cut out and replaced with carbon fibre wraps and other supplementary strengthening methods to restore the tensile strength of the bridge.
Getting new concrete poured can be expensive, and it also takes time for the new concrete to cure properly. For many of our clients, this just isn’t practical. Fortunately, there are several effective concrete repair solutions that can be used to speed up the process and reduce the costs associated with new construction. One of these is epoxy injections, a concrete repair method that uses a special polyurethane compound to fill cracks and voids in the concrete.
Drilling and plugging is a simple repair method for concrete surfaces that can be used to widen cracks and seal them. It involves enlarging the crack and filling it with a joint sealant. This technique is not as effective as epoxy injection for major structural repairs. It is also not suitable for wet cracks unless they are injected with moisture tolerant epoxy.
This method is best suited for cracks that appear in straight lines and are not leaking. It involves drilling a hole close to the crack and then filling it with grout. This grout acts as a key that locks the crack and prevents further expansion. It also helps to prevent leakages and loss of soil.
There are several different methods of repairing cracked concrete structures. Choosing the correct method for the job requires careful evaluation of the structure. Successful repair procedures must take into account the causes of the cracking. For example, if the cracking is due to drying shrinkage then it is likely that after a period of time the cracks will stabilize. However, if the cracks are caused by ongoing foundation settlement then the cracks will not repair until the settlement problem is addressed.
Several methods of repairing cracks in concrete have been developed and implemented. The most common ones include routing and sealing, stitching, external prestressing and epoxy injection. However, it is important to remember that if the cause of the cracking has not been corrected, then the cracks will continue to expand and may eventually lead to failure of the concrete.
Dry pack mortar is a strong sand & cement mixture that’s typically used for masonry repair work. It’s made by mixing Portland cement with sand, and then just enough water to hydrate the cement. It’s sometimes referred to as deck mud or floor mud, and it’s a great material for repairing cracks that are deeper than they are wide. It’s also often used to create a thick bed of mortar for tile, brick or stone placement.
Before making any repairs with dry mix, it’s important to clean the surface that needs to be worked on. This should include removing any loose particles with a wire brush or vacuum cleaner. Next, the area should be soaked overnight to pre-hydrate it. This will help to reduce the amount of shrinkage that occurs when the concrete dries.
Once the area is hydrated, it’s ready to be repaired. It’s best to work with small batches, as too much mortar at once can be difficult to maneuver and compact. Once the mortar has been applied to the desired area, it should be thoroughly compacted using a hardwood stick with a hammer. It’s recommended that compaction be performed every few inches to ensure a tight, dense mortar. It’s also helpful to apply a waterproofing compound after completing the repairs in order to protect the new concrete from damage caused by moisture. This can be done by a professional or purchased pre-mixed from a hardware store.