When the Interstate Highway System created a need for thousands of new bridges, prestressed concrete became an industry.
Concrete Contractors Colorado Springs strengthens concrete against the tensile forces it will experience in service.
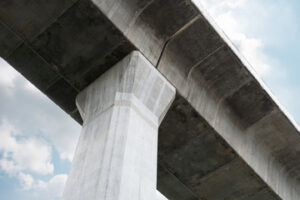
It does so by placing steel tendons (wires or cables) under tension within the concrete. The tendons are then anchored.
In pre-tensioning, steel bars or wires are held under tension inside the concrete structure before it is cast. This process is especially useful for long-span structures such as bridges and girders. The tension in the steel is used to counteract the tensile stresses that the external loads on the structure would otherwise generate. Pretensioning allows for more efficient use of materials and provides for better structural performance.
Conventional reinforced concrete relies on reinforcing bars to cater to the tensile stress induced by the imposed load. However, this method requires large amounts of material that increases the weight and cost of the structure. In addition, the concrete’s lack of tensile strength limits its ability to span between piers. This is why prestressed concrete is used in large, long-span structures.
For example, a pre-tensioned concrete beam can support a large amount of weight between two piers because it is supported by tendon compression. Pretensioning also makes it possible to build lighter structures that require fewer columns or struts, which would be impossible with conventional concrete.
The tendons are directly bonded to the concrete (internal prestressing) or placed within a sheath or duct within the concrete section (post-tensioning). Post-tensioning is often preferred when the structural element has to be transported or when installing the elements before casting is difficult.
Both methods have advantages and disadvantages. Internal prestressing is ideal for precast production because it can be easily performed in factories. It is also more economical and simpler than on-site posttensioning. However, if the structure is large or needs to be transported, it may be more effective to use on-site post-tensioning.
Prestressed concrete is made by applying a compressive pre-load to the concrete using tensioned steel wires, cables, or rods. The resulting concrete has no tensile stresses under working loads and is often much stronger than equivalent cast in-situ concrete. This can be achieved by putting the steel in tension before the concrete is poured (prestressing), or the steel can be put in place and then tensioned after the concrete has set and bonded to it, known as post-tensioning.
The advantage of this method is that it reduces the amount of concrete needed, so taller buildings can be constructed without using an enormous amount of material for each floor. It also means fewer areas for cracks in the structure, making it more durable.
Concrete is strong in compression but weak in tensile forces, so post-tensioning helps to compensate for this weakness. Creating concrete components that are thinner and longer than likely with conventional construction methods is possible, enabling innovative architectural designs. It also increases the mechanical resistance of concrete elements and reduces deflections and vibrations in structures.
Post-tensioning can create structural elements in various applications, including bridges, slabs, and foundations. It’s most commonly used in large, long-span structures that require heavy loading. The technique can also improve the seismic performance of existing concrete structures.
The most important aspect of a successful post-tensioning project is determining how much stress and when to apply it. Too little stress will result in premature failure of the prestressed concrete, while too much will lead to cracking and damage. This can be difficult to calculate accurately, so it’s important to consult a professional engineer when designing and building a prestressed concrete structure.
There are two different types of post-tensioning systems: bonded and unbonded. Bonded post-tensioning involves using a sheath injected with cementitious grout or liquid wax before it’s embedded in the concrete. The sheath protects the tendons from contamination, which can affect their strength and durability.
Unlike normal concrete that is brittle under compression, prestressed concrete can absorb and transfer the force of compressive loads through high-strength steel cables (referred to as tendons). These tendons are usually made from single wires or multi-wire strands and are anchored to both sides of the concrete. This allows the concrete to elongate under compression, which increases its structural efficiency and serviceability.
Prestressed concrete involves pretensioning the steel cables before pouring and curing the concrete. During the pretensioning process, lengths of steel wires are placed in an empty formwork and then stretched, and anchors are inserted. The tendons are then surrounded by concrete, which is then poured and allowed to cure. Once the concrete has cured, the tendons are released. Since they are already under tension, the concrete is compressed.
Another method of prestressed concrete is post-tensioning, which involves placing the tendons in the casting bed and removing the formwork after the concrete has been set. During this process, the high-strength steel is not exposed to the elements, which reduces the risk of corrosion. The tendons are pulled to develop the desired level of tension and anchored against casting bed abutments.
Both methods of prestressed concrete have advantages over conventional concrete, including increased load capacity and flexibility. In addition, the concrete can be poured and cured to a thinner section than in traditional construction, which saves time and money on-site. This slender design also increases usable floor space and makes buildings, shopping centers, and parking garages more attractive.
The disadvantage of prestressed concrete is the initial loss of force during transfer, which can be as much as 20 percent of the force applied. This loss can be due to the elasticity and creep of concrete, friction in the ducting and tendons, and other factors.
A high-strength grout may reduce the loss of tension during the transfer of forces. However, this can cause an increase in the cost of the concrete. The use of high-strength grout can also lead to a decrease in the serviceability of the concrete, which is why the concrete must be designed correctly. This includes considering the effects of temperature and humidity on the material. Fortunately, numerous professional organizations are dedicated to prestressed concrete that can help design and construct buildings and other structures using this innovative construction method.
The most critical portion of a post-tensioned concrete member is the anchorage zone. It carries high tensile forces and must be designed to prevent failure. A considerable amount of research has been undertaken to understand the behavior of this zone and to calculate bursting tensile forces effectively.
The anchorage consists of a bonded tendon length in direct contact with concrete. It is generally located at the end of the member’s section. Several different anchorage systems are available, depending on the requirements of each project. The most common system is the CPS stressing anchorage. It comprises a square or circular anchor plate with 8 or 12 tapered holes for the prestressed wires. Each hole carries a wedge-shaped segment of the flat surface of a split cone, which grips the wire and locks it into the anchor plate. This anchorage is used in long-span structures such as bridges.
Another type of anchorage is the tube unit. This system is more compact than the CPS stressing anchorage and consists of a fabricated steel component with a thrust plate, a U-plate, and a spiral. It can be used for horizontal and vertical applications and is suitable for use with steel strands bonded to the sheathing. It is also easier to inspect and replace than the CPS stressing anchorage.
A hydraulic jack is used to apply the desired amount of tension to the wires for pretension. The bulkheads at each end of the duct are then gripped by wedge-shaped segments of a split cone, which transfer the prestress from the tendons to the concrete. The duct is then grouted.
A third method of pretensioning is the Shorer system. It uses a central tube of high-strength steel to carry the prestress from surrounding wires. The tube is then removed after the concrete has achieved sufficient strength. The cable is then anchored to the concrete with a shear connector, and the connection is sealed with a cement grout.
When a member is stressed, many transverse tensile stresses are generated in the tendons. These stresses must be transferred to the concrete to avoid bursting failures. The tendons must be anchored in the anchorage to ensure that they can resist these forces. This is important for the safety and durability of a structure. The anchorage zone must be designed to withstand these forces, and a good understanding of the physics of tensile stresses is essential for its design.